Lean Management Tools and Techniques
Lean Tools
Traditional Lean Tools and Techniques
“Where to start?” or “What to do next?” are frequent questions asked during Lean deployment. However, unlike other improvement methodologies, there is no prescribed “Lean Path”.
Instead Lean offers a tailored approach, which makes it more likely to find a solution that meets your business’s unique needs. On the other hand this process can seem more difficult, as you have to plot your own journey. We can help you decide which Lean tools and techniques are most appropriate to use, and also (most importantly) at which time.
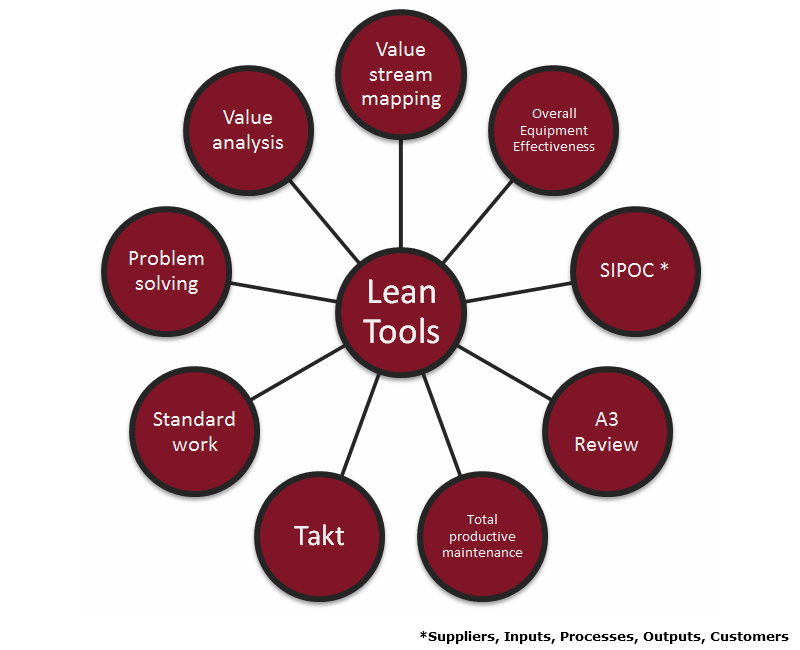
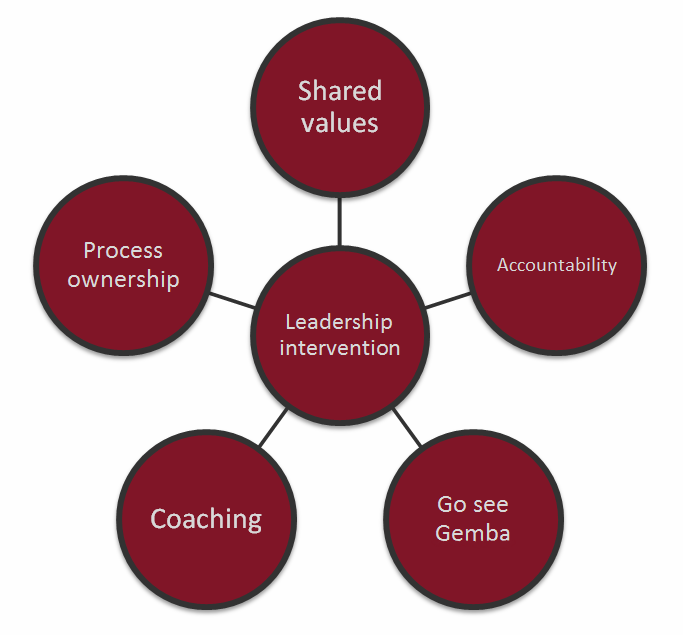
Leadership Intervention Mechanisms
The role of leadership has been identified as a key component of successful Lean management. The scale of intervention required is often underestimated, not so much initially, but after 12-18 months when the initial velocity has slowed to a more sedate pace and other business pressures have started to take over.
We can help you put leadership strategies in place to sustain and grow the deployment, and ensure your leaders’ support of the new system is as relentlessly as the system itself.
Employee Involvement
Employee Involvement and Engagement Systems
One of the main barriers to successful Lean management is a failure to deploy employee involvement and engagement systems effectively.
We have often seen significant effort and resources being placed into Kaizens and mapping events only for the initial burst of improvement to fade away over a period of time. One reason for this improvement degradation is the lack of a supporting employee system.
We can help you set up, test and implement the best employee systems for you.
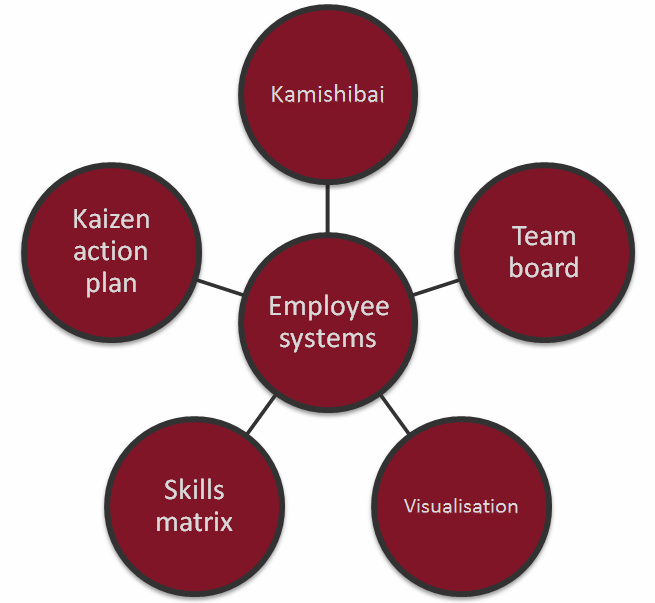