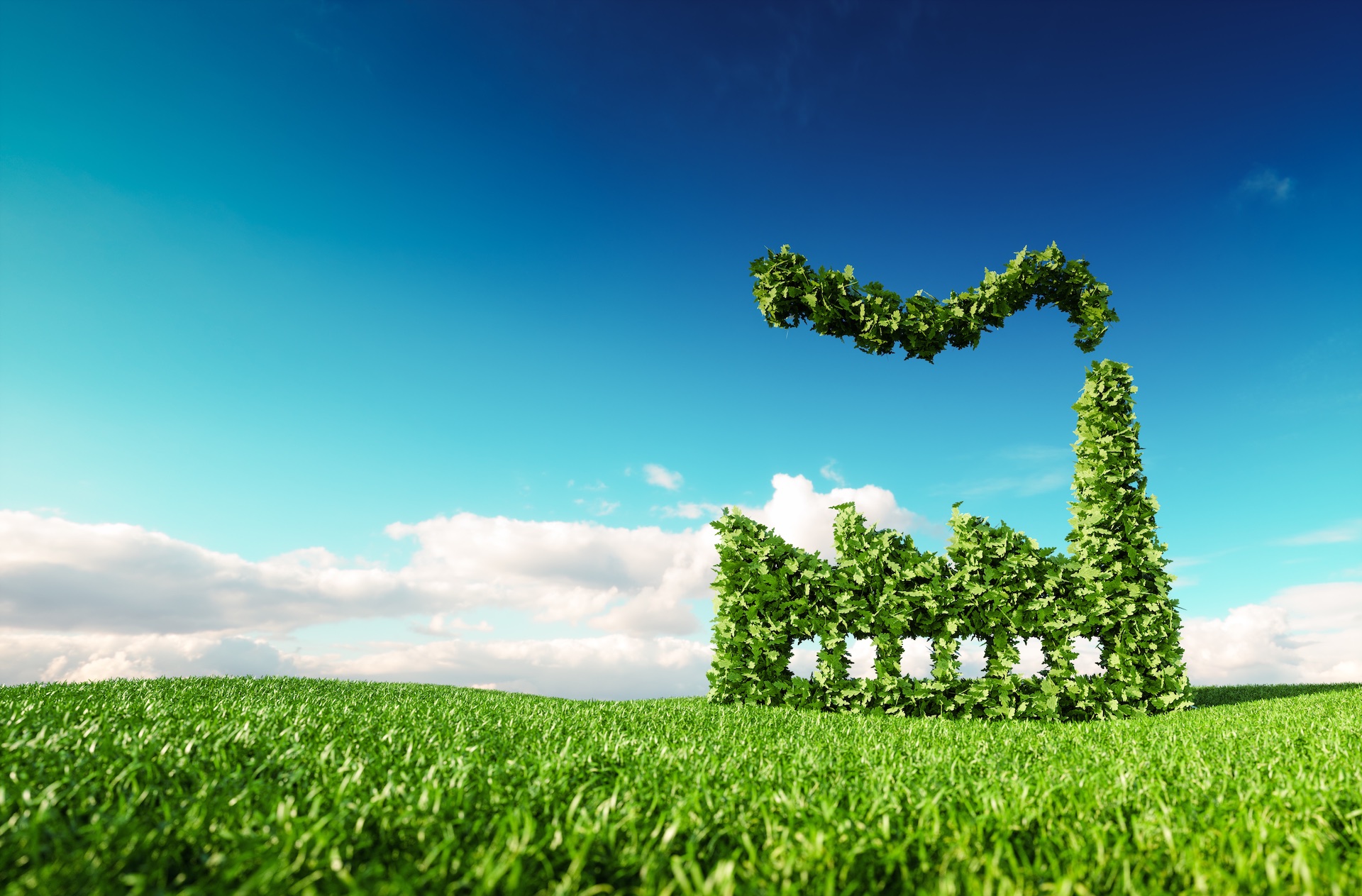
Moving To A More Sustainable Manufacturing Operation
There has been a lot of publicity and discussion about COP 26 and the need to avoid further global warming through the reduction of CO2 and other environmental wastes. Whilst this has provided motivation and a vision, there is still much work to be done in the manufacturing sector to become more sustainable, especially within existing operations.
Many manufacturing companies have already embraced the Toyota Production System through the deployment of Lean manufacturing principles. This provides an excellent foundation to move from Lean production to sustainable production.
Step 1 – Select The Environmental Value Stream
The first step provides direction and purpose to the improvement activity. Identification of a stable value stream ensures that there are no other distractions to the improvement activity. Though previous clients were keen to have more sustainable production, we were presented with seemingly stable Lean production which subsequently became un-stable, diverting management and operator efforts to maintain the basics of quality and output. The Lean production also needs to have a significant use of environmental resources and impact.
Clearly, the more resources you use and waste the more opportunity there is for sustainable production. The final piece of the set up is having committed leadership and employees who want to be more sustainable in their work, like Lean production, a sustainable production initiative will fail without leadership support and coaching.
Step 2 -Identify environmental aspects
The second step aligns the activity to the current move towards more sustainable manufacturing given by a customer value in this area. Many customers are making sustainable production a pre-requisite for supply and will also use this as a selling point for their products. The activity needs to align to strategy or be linked to close a performance gap. This provides the connection to objectives (either personal or performance) to reduce the environmental impact of the operation.
Step 3 – Measure the environmental value stream
The third step commences the real work of achieving sustainable production and starts with the collection of data for the environmental value stream. Whilst this may appear straightforward, it can be quite challenging. A walk into the Gemba will help to identify the environmental flows and what needs to be measured. This subsequently may initiate the collection of data for previously unidentified environmental flows. Several of our clients had to pause their green projects whilst the data was collected for all their E- flows.
As with any improvement activity, the opportunity is taken to capture any wastes and issues that are surfaced during the data capture activity.
Step 4 – Kaizen
Once the pre-work of data collection has been completed, the full team can be assembled to map out the environmental value stream.They identify the wastes and issues to help create the future state. This is a very visual exercise and should be completed using the traditional brown paper and post-its. This helps to achieve engagement and buy-in from the team.
Step 5 – Continuous Improvement
The final step creates the pathway to implementation through the development of a vision and an action plan. The plan will identify the steps to the vision, resolve the issues uncovered in the activity and set the steps to reduce the environmental impact of the operation. After a year, it’s appropriate to review the status of the sustainable production value stream and run the kaizen again – maybe not to its full extent but a mini – review to tweak and improve the operation.
If you need help with making your value stream more sustainable then please contact:
E: neil.trivedi@theperfectprocess.co.uk
E: getintouch@theperfectprocess.co.uk
T: + 44 (0) 7758 953366
W: theperfectprocess.co.uk